Van Oord Inks Service Agreement with ABB Turbocharging
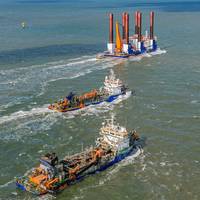
Dutch dredging company Van Oord signed a three-year agreement with ABB Turbocharging to provide fleetwide maintenance and optimization services. The agreement comes as two Van Oord vessels receive the first turbocharger upgrades of their kind in the dredger sector, an upgrade at saving fuel and carbon emissions over the next decade.The service agreement, which marks more than 30 years of cooperation between Van Oord and ABB Turbocharging, is designed to help the owner minimize lifecycle costs and improve emissions across its fleet.
Interview: Dirk Balthasar, President, Thermamax
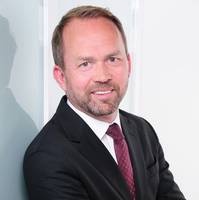
To start, can you give an overview of the Thermamax offering to the maritime industry?Thermamax is a specialist in the design and manufacture of thermal and acoustic insulation solutions for diesel engines, spark ignited engines, exhaust aftertreatment systems and electric storage systems. Our markets include automotive, on- and off-highway sectors, power sports vehicles, stationary power generation, ships, and oil platforms, both on land and at sea. For the marine industry, Thermamax is a solution provider for SOLAS-compliant insulation solutions for engine rooms.
CMR Instrumentation, Sensor Control for French Navy Newbuild
CMR GROUP, the marine automation and instrumentation specialists, has supplied the French Navy’s latest maritime patrol vessel with advanced marine condition monitoring and sensor equipment. The deal sees a fully integrated instrumentation and sensor control platform specified for the Light Patrol Vessel La Confiance, in a move that reflects CMR’s continuing expansion in the sector as one of the leading designers and suppliers of next generation marine technology. Built at the SOCARENAM shipyard, the vessel is the latest addition to the French fleet and will undertake operational activities and patrols throughout the Caribbean from its permanent base in French Guiana.
WSS: Post-combustion Fuel Treatment Cuts Vessel Costs, Risk
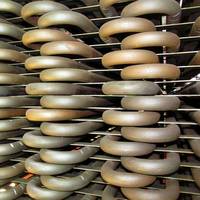
Wilhelmsen Ships Service, a provider of products and services to the shipping industry, is advising vessel operators to wage war on soot. According to WSS, soot accumulation in a ship’s exhaust gas boiler (EGB) is a serious issue, leading to reduced EGB efficiency, significant cleaning costs, corrosion, and the risk of soot fires. However, a simple post-combustion fuel treatment can solve all these problems, at negligible cost. Refined heavy marine fuels are full of contaminants, such as Vanadium, Sodium, Aluminium, Silica, and Potassium, which leave deposits when burnt.
New Diesel Soot Filtration System
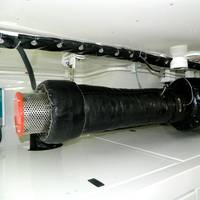
Problems caused by inefficient regeneration of a Diesel Particulate Filter (DPF) can be eliminated with the installation of a SeaClean Soot Filtration System (shown above) by marine exhaust system engineering, design, fabrication and service company DeAngelo Marine Exhaust. The SeaClean system monitors the exhaust gas temperature and varies the power going to the heater element so that exhaust gas temperatures are constant. This allows a DPF to work properly so that collected soot is burnt off at high temperature, leaving only a tiny ash residue.
A Closer Look inside the Alfa Laval Test & Training Center
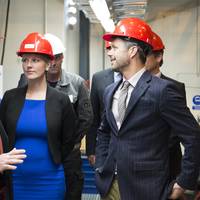
Just two months remain until the inauguration of the Alfa Laval Test & Training Center on January 15, 2014. Originally conceived for the development of PureSOX and other emission control technologies, it has grown to incorporate far more than just exhaust systems. Now that the majority of the equipment is in place, it is possible to take a deeper look into the details of this remarkable new facility. Located on the site of the former Aalborg Shipyard in Aalborg, Denmark, the new Alfa Laval Test & Training Center is an imposing structure.
Alfa Laval Tumba AB at Nor-Shipping 2013
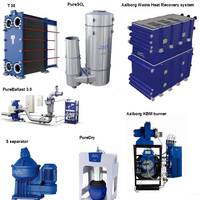
Taking place June 4-7 at Norges Varemesse in Oslo, Nor-Shipping is an international forum for Northern European maritime industry. At the Alfa Laval stand in Hall E, visitors will find a comprehensive approach to easing financial and regulatory pressures, with solutions for energy efficiency and extending performance at the forefront. Today’s marine industry faces difficult and conflicting challenges, especially when it comes to energy. As rising fuel prices and shrinking margins create a push to reduce fuel consumption…
LCAC 91 Achieves High Speed on Algal Blend
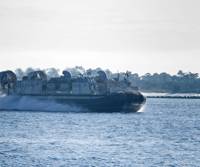
The U.S. Navy successfully concluded its final alternative fuel demonstration for the year today with the Dec. 7-9 operational tests of the 50/50 algae-derived, hydro-processed algal oil and petroleum F-76 blend in a Landing Craft, Air Cushion (LCAC) amphibious transport vehicle at Naval Surface Warfare Center Panama City. The tests also marked the fastest speed achieved to date by a U.S. Navy surface craft using alternative fuel blends, as LCAC 91 reached speeds the crafts maximum speed of 50 knots, Dec.
LMS Wins RFA Ship Refit Contract
The Ministry of Defense has awarded a contract to Litton Marine Systems to install an ISIS 2500 alarm monitoring and condition assessment system on the auxiliary supply ship RFA Ft. Rosalie. The new order follows on the successful sea trials of a similar system on the sister ship, RFA Ft. Austin, earlier this year. As with the installation on RFA Ft. Austin, Litton was required to complete the installation in under seven working days, during which the ship will be in a four-hour readiness status. The installation was scheduled for completion in December 2000. The scope of work will include removal of the existing system, installation and commissioning of the new equipment, technical support and onboard crew training.