Multiple Failures Led to Pacific Khamsin Drillship Fatality
Multiple training and personnel safety failures led to a 2020 worker casualty on board the Pacific Khamsin drillship in the Gulf of Mexico, the Bureau of Safety and Environmental Enforcement (BSEE) said in a recent report..A rig crewmember was killed on August 23, 2020 while assisting his team in breaking out bolts and pulling riser joints to the surface as the Pacific Drilling drillship crew prepared to secure the well and evacuate the location ahead of incoming storms. The drillship was under contract with Total E&P USA, conducting well operations in Garden Banks Block 1003, approximately 174 miles offshore Louisiana at the time of the incident.A panel comprised of BSEE subject matter experts…
Subchapter M: Post Publication Highlights
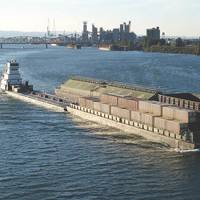
An extra T in TSMS, nowhere left to hide from systems documentation, and an emphasis on continuous improvement. Back in January of this year, the United States Coast Guard (USCG) predicted Subchapter M would be released in spring 2016. I put my money on June 20, that being the very last day of spring, and on June 20 the long-awaited regulation was finally published. Subchapter M doesn’t come with much we weren’t expecting, which is a good thing. Surprises in this industry are not met with enthusiasm. The USCG should be complimented in that regard.
Cadets See Benefits of ISM-certified Training Ship
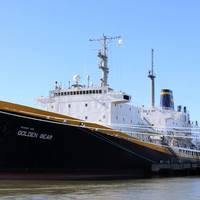
Two years after Cal Maritime became the first U.S. maritime academy and training ship to be certified for the International Maritime Safety Management Code, cadets at the academy are seeing the benefits. “The most compelling part of this story is how the cadets have so quickly adapted to the ship’s Safety Management System (SMS),” said Harry Bolton, captain of Cal Maritime’s training ship Golden Bear. “Prior to any work being done aboard the ship, the cadets – with direction from the faculty supervisor – fill out a Job Safety Analysis (JSA) form…
Making Stop Work Authority Work
It is one thing to have a policy posted. It is another to review and explain such a policy to a new crew during their orientation or when they first sign on a vessel. And, finally, it is still another to claim the policy has been effectively implemented. A number of recent maritime incidents have led to ‘Stop Work Authority’ (SWA) becoming a federally mandated part of a safety management system (SMS) for vessels operating in certain areas and industries. Other sectors, while not federally mandated with respect to this requirement, adopted and implemented SWA years ago, on their own. SWA, far from a new concept, is one that recognizes the importance attached to encouraging any employee on board a vessel (whether licensed…
Rig Moves: Mobilized for Performance
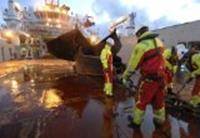
The operation of an oil field involves moving rigs or jackups in a maneuver referred to as a rig move. These complex operations require experience and the coordination of all stakeholders. Explanation by Pål-André Malø, superintendent for new construction, and former AHTS captain (Anchor Handling Tugs Supply) with Bourbon Offshore Norway. "Generally speaking, this operation mobilizes between 3 and 4 vessels tasked with pulling the anchors of the rig to position it. Most of the time, there are 8 anchors - sometimes 10 or 12 - weighing 6 to 20 tons each," Pål-André explains.
Is it Safer to Work Offshore in 2013?
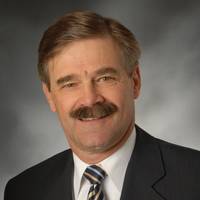
It has been over three years since the tragic accident occurred aboard the Deepwater Horizon on April 20, 2010. The industry and the relevant federal agencies have done much to put in place improved safeguards to prevent such an accident – which left 11 dead and 17 injured – from happening again. Congress, on the other hand, has done little to intervene to force new requirements on either the federal government or industry. Meanwhile, energy-related work in the Gulf of Mexico is rapidly increasing and forecasts are that it will remain busy for the next few years.
Insights: Gary Faber
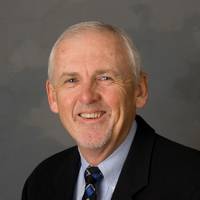
Gary Faber brings more than 30 years of experience in the maritime industry to the position of president and COO of Foss Maritime Company. His extensive experience in marine engineering, vessel operations, salvage and project management in extreme environments extending from the arctic regions of Alaska all the way to the southern extremes of South America frame perfectly the diverse workload of this Seattle-based marine services firm. His notable accomplishments include recognition for the U.S.
SafeOps: Dredging Industry Full Ahead
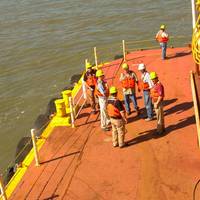
Safety experts both in and out of the maritime industry have for years been urging companies to restructure their organizational charts and erase the traditional division between Safety and Operations Departments in favor of disseminating safety responsibilities throughout operational divisions. This internal merger is often sold as an effective strategy for improving employee communications, fostering greater safety leadership throughout a company, and reducing the rate of injuries, as well as the high costs that come with them.
Make an Auditor Happy: Keep your files tidy and your papers dirty
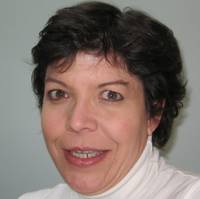
File names are important when it comes to compliance auditing of safety management systems and document control. Attaching reports and sending via email, once a costly proposition, is now an effective and quick means to get data from the ship to the office in a much timelier and trackable way. But, have you thought about how to name these files so that once they’ve all been received they’re easily sorted and retrieved, both in the office and onboard? There is nomenclature, special terminology, which carefully names the parts of the vessel.
Port Hamburg Cargo Handling Increases Again
Hit hard by the global financial and economic crisis in the year 2009, the Port of Hamburg reports total cargo-handling figures of 28.6 million tons for the first quarter of 2010, an increase of 4.6 per cent over the same period in the previous year. On the import side, Port of Hamburg Marketing – the marketing organisation of the Port of Hamburg – recorded cargo-handling figures of 16.7 million tons (+6.0 per cent). Exports via Hamburg also increased in comparison with the first quarter of 2009, with a total of 11.9 million tons (+2.7 per cent). General cargo handling, the dominant segment in Hamburg, returned to growth (1.1 per cent) with a total of 18.6 million tons.
Q&A on Offshore Safety
MarineNews: How long has your current safety training program been in place? Bruce Adams: The current Schlumberger New Employee Safety Training program (NEST), was developed in 1991. This is a six day, intensive training course covering a variety of mandatory safety topics. In 1992, the National Ocean Industries Association (NOIA) recognized the program as the best overall training program in the offshore industry and awarded Schlumberger the NOIA "Safety in Seas" award for 1992. MN: How much money is spent annually on the safety program? Adams: The NEST program is part of a much more comprehensive safety effort in Schlumberger. From 1996 to 1998, the amount of money spent on safety by Schlumberger in the US alone increased from $12.4 million to $19.4 million annually.
Q&A on Offshore Safety
MarineNews: How long has your current safety training program been in place? Tom Knode: Halliburton Energy Services and its predecessor companies have conducted safety training for employees for at least the past three decades. MN: How much money is spent annually on the safety program? Knode: The safety program, including safety professionals, equipment, training, and auditing, runs into the tens of millions annually. MN: Is the program conducted in-house? Or are the employees sent to an off-site facility? Knode: The majority of safety training is conducted in-house. MN: If in-house, is the program taught by staff members? Or is a third party brought in for instruction? Knode: The training is primarily conducted by our training and safety professionals.
Offshore Industry Leaders Invest Heavily In Safety Programs
The offshore oil industry market, by its very nature, is a challenging work environment that poses many safety hazards, particularly for individuals and companies which lack adequate safety training. Maritime Reporter & Engineering News sought the insight of two offshore industry leaders — Schlumberger and Halliburton — to discover how the industry leaders set the stage for a work environment that is safe for workers, equipment and investment. Note: Participants in the survey were Bruce Adams, the QHSE manager for Schlumberger Oilfield Services; and Tom Knode, the HSE Manager for the Business Development segment of Halliburton Energy Services. MR/EN: How long has your current safety training program been in place?